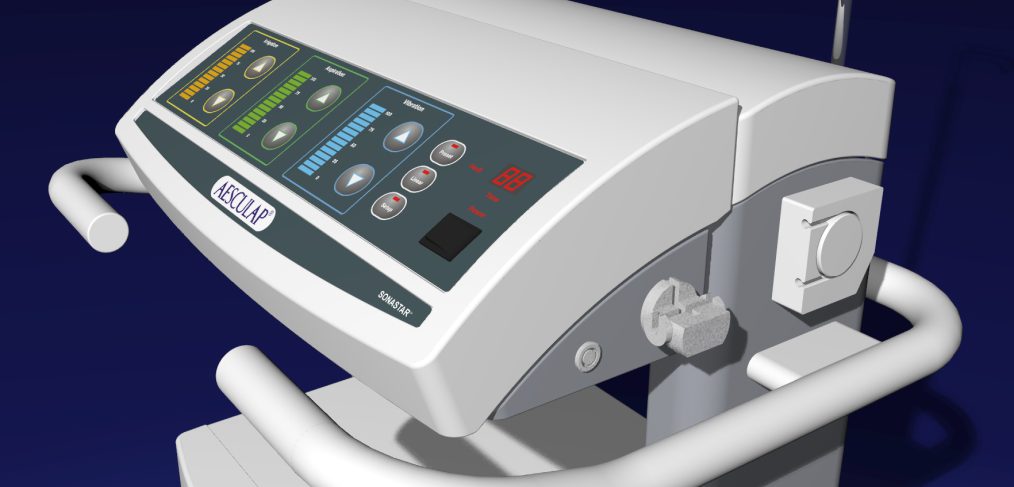
Case Study: Ultrasonic Aspirator
SONASTAR Ultrasonic Aspirator System
for Misonix, Inc.
The SONASTAR Ultrasonic Aspirator is a multifunctional system designed to fragment, emulsify, and aspirate soft tissue while leaving healthy tissue intact. It is used for tumor removal in neurological, spinal, gastroenterology, urological and many laparoscopic surgical procedures. This product generates and delivers an electric signal to a handpiece used by the surgeon to disrupt necrotic tissues. It also provides pumped irrigation fluids and suction to aspirate the tissues via a cannula into a specimen container.
The objective of this project was to re-package the existing components of an outdated and costly unit in time for an industry trade show. The product assembly was methodized for cost reduction as well as modularity for an easy-to-handle sales version that could be placed in the trunk of a car, and a desktop version for lab use.
Primarily used in a surgical theater, one of the key functional requirements was quiet, low-noise operation. After extensive research and multiple concepts (including a rotationally-molded construction), the noisy aspiration (vacuum) pump was housed in a sheet metal compartment in the lower portion of the unit with a separate muffler compartment for the air intake (from underneath) and exhausting out fans in the rear. All interior surfaces of the pump and muffler compartments were covered with a composite sound-absorbing foam.
Completed in three months, the program included the construction of several fully functional prototypes in addition to the complete production database for the floor, desktop and sales units. The final build incorporates several materials and manufacturing processes:
• Pressure Formed Acrylic/PVC (covers)
• Aluminum Extrusions with Custom Machining (uprights)
• Aluminum Sheet Metal Construction (base and controller chassis)
• Bent Aluminum Tubing (handle)
• Custom Machined Aluminum and Acetal Components (wheel and filter assemblies)
Pressure Formed Covers and Machined Details
Drawings and Tooling for Pressure Formed Covers
Sheet Metal Base Chassis
Machined Aluminum Extrusions for Modular Assembly
Services:
- Concept Development
- Industrial Design
- Plastic Piece-Part Design
- Pro/Engineer Database Development
- Project/Client Management
Deliverables:
- Complete Production Documentation
- Product Graphics and Production Files
- 3D File Exports for Production
(Note: This project was completed by Warren Ginn while an employee of Integrated Design Systems. Visit www.idsys.com for more information.)